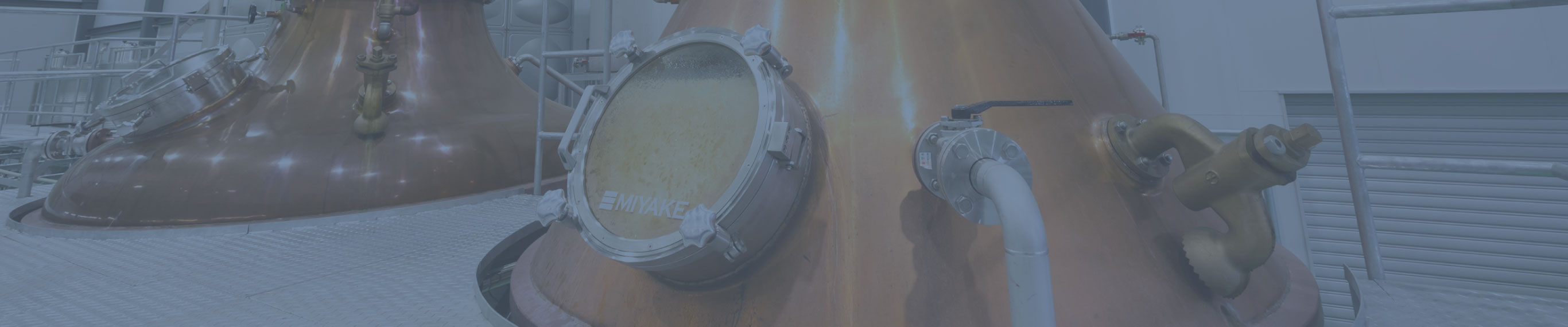
Sectors / ProductsDistilling【Our Achievements】Distilling Equipment
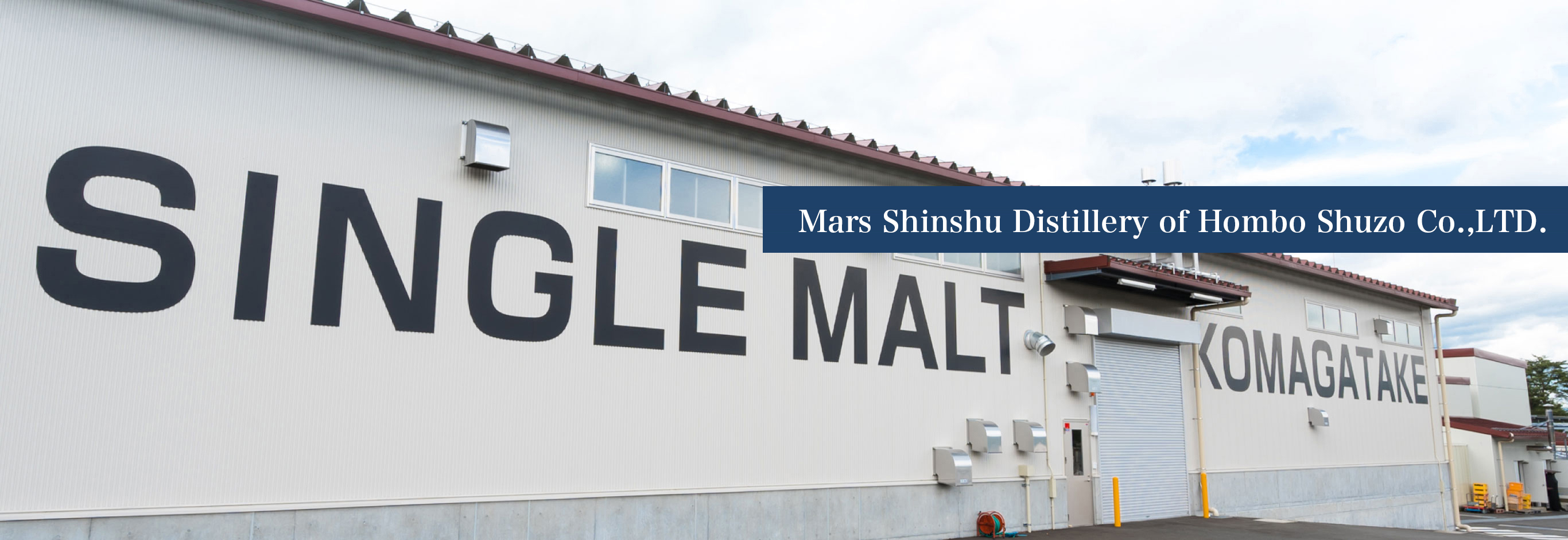
Nestled in resplendent nature at the foot of the Central Alps, the Mars Shinshu Distillery produces Shinshu whiskey at an altitude of 798 meters. MIYAKE has been contracted to manufacture equipment for this distillery since its opening. The MIYAKE brand’s technology is still alive there even after the full-scale renovation in 2020.
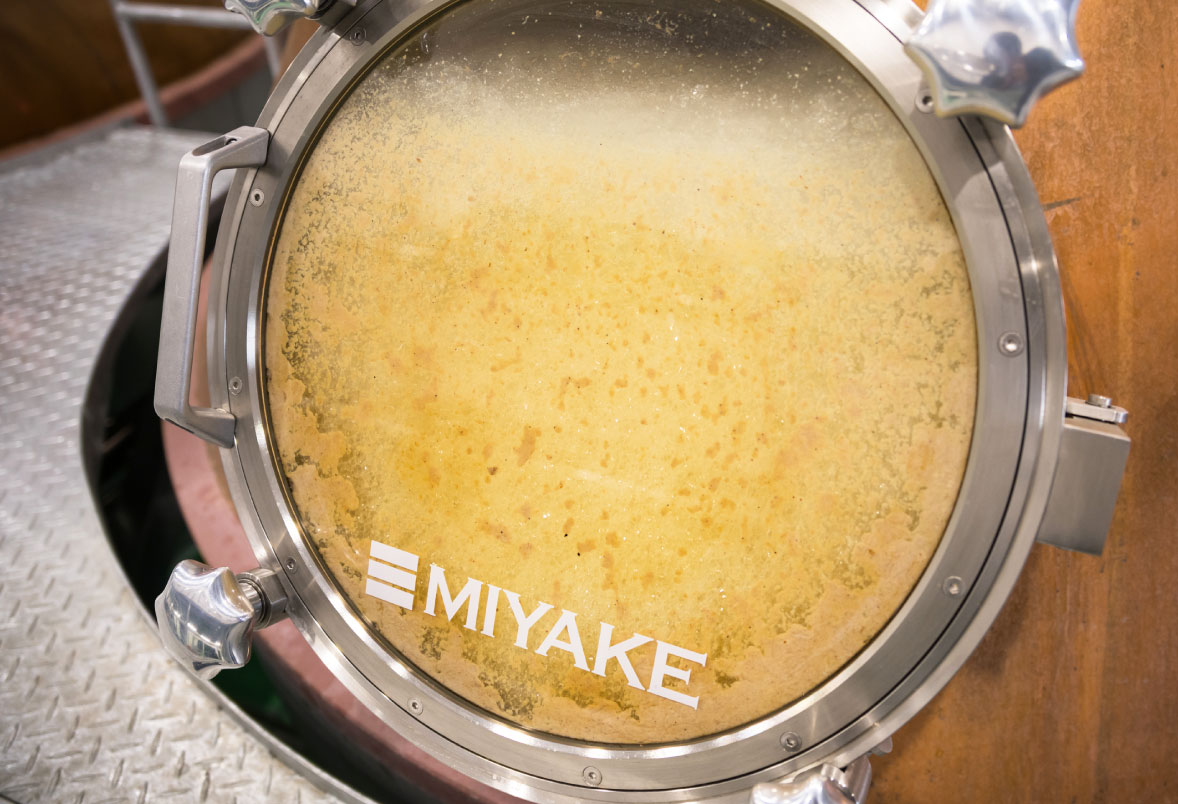
Reopened in 2020 after renovation amid the growing appreciation for Japanese whiskey
It was in 1949 that Hombo Shuzo, which had been dedicatedly producing shochu in Kagoshima, acquired a license to produce whiskey. In 1960, they opened a factory for wine and whiskey production in Yamanashi, and in 1985, they completed the Mars Shinshu Distillery at 798 meters above sea level, at the foot of Mount Komagatake in the Central Alps, in the village of Miyada in the Kamiina district in Nagano Prefecture, in search of the best environment for whiskey production.
Although they were forced to suspend their operations in 1992 due to a sluggish demand for whiskey, they decided in 2009 to restart distillation as Japanese whiskey began to be appreciated worldwide. At that time, they asked MIYAKE, which was contracted to manufacture their whiskey distilling equipment when the distillery was opened, to reorganize the equipment. In 2010, they restarted their operations.
They also asked us to be involved in the renewal of their distillation stills in 2014 and their large-scale renovation in 2020.
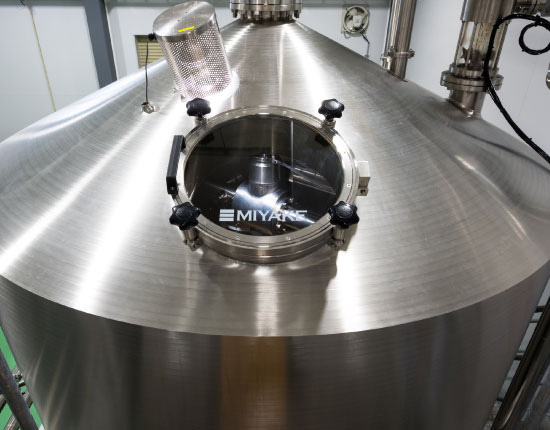
MIYAKE is the only company
with the ability to manufacture process equipment as a whole in Japan
At the time of the reopening in 2010, we replaced some parts of the equipment, such as condensers attached to the pot stills. In 2014, we installed new pot stills, which are the cornerstone of the distillation process. Our mission was to “reproduce the same taste as the distillery produced at the time of the opening.” The shape of pot stills has a great influence on the taste of whiskey. Since the drawings of the original pot stills were not left, we started from measurement and manufactured them, aiming for the same shape and taste.
In 2019, a more extensive full-scale renovation took place to refurbish aging equipment and maintain the barrel storage equipment in anticipation of increased whiskey production. During the renovation, the distillery newly built a whiskey distillery building, where visitors can observe the production of whiskey, and a visitor's building, where original whiskey and goods can be purchased, along with refurbishing the existing equipment. We were contracted for the equipment for process production from malt crushing to mashing, filtration, fermentation, and distillation, and the renovation was completed in September 2020. Thus, MIYAKE is the only manufacturer in Japan with the ability to undertake the engineering and manufacture of equipment as a whole.
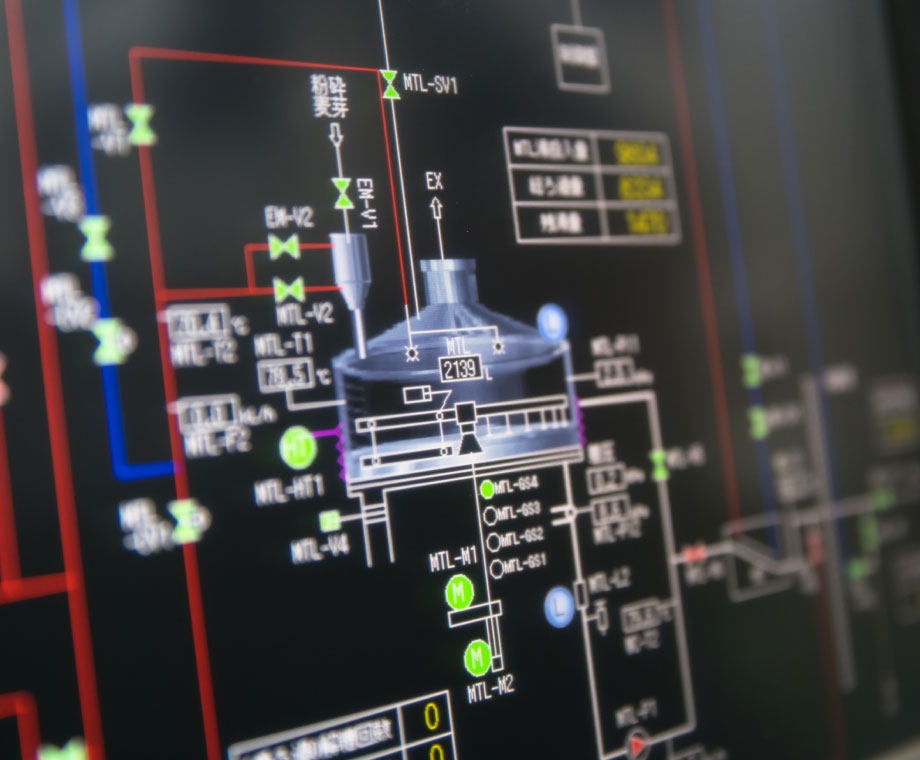
Improved operability in each process to achieve manpower savings and workload reduction
Among the equipment we were contracted for this time, there was a malt crushing machine manufactured by Künzel in Germany. It is our strength to be able to provide, in-house, not only assembly but also perfect maintenance, whether or not it is of our product.
The rest of the equipment was our unique custom-made products, including mashing tanks (Lauter tun) and stainless-steel fermentation tanks. The use of build-to-order manufacturing, with its high degree of freedom in the shape and arrangement of equipment, enables us to manufacture products that meet customer needs, which is our advantage. In addition, to meet the customer’s request for “manpower savings,” we developed a system that partially automated operations and significantly improved operability in each process. During the development of the system, we made proposals not only on the equipment we were contracted but also on other equipment and the building layout based on our know-how and experience from working on many distilleries, which was appreciated by the customer. Our support for post-delivery maintenance and troubleshooting is also perfect.
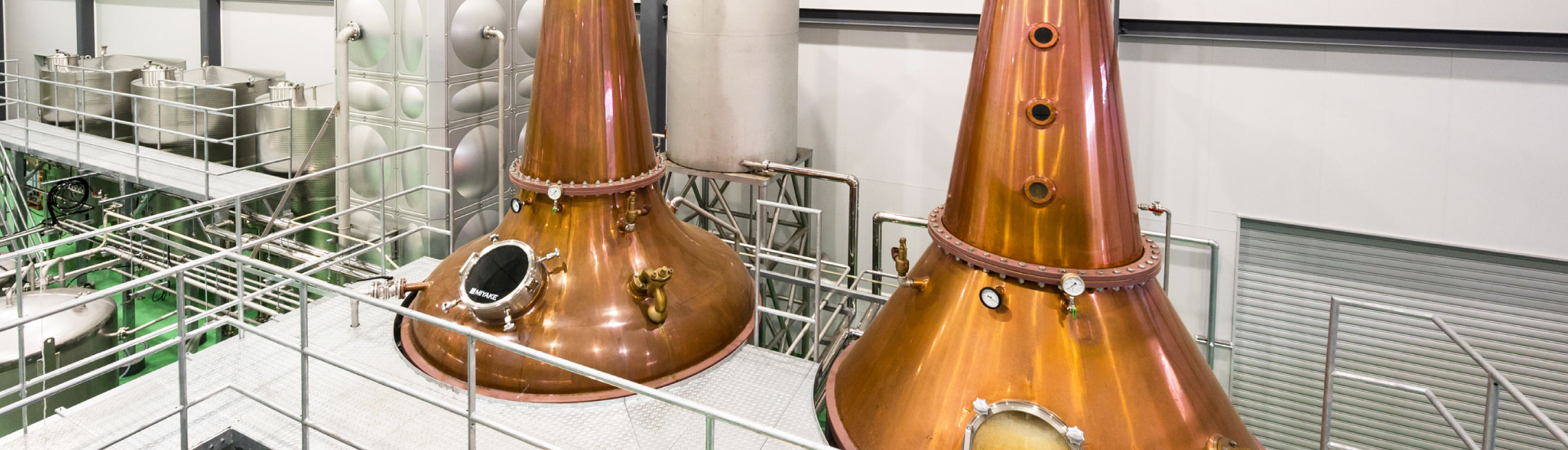
Words of gratitude from the customer include these: “The improvement in operability enabled us to pursue a higher level of liquor quality due to manpower savings and significant workload reduction” and “With the first full-scale renewal in 35 years, we were able to make a fresh start as a production base that spreads the appeal of the Mars Whiskey more deeply.”
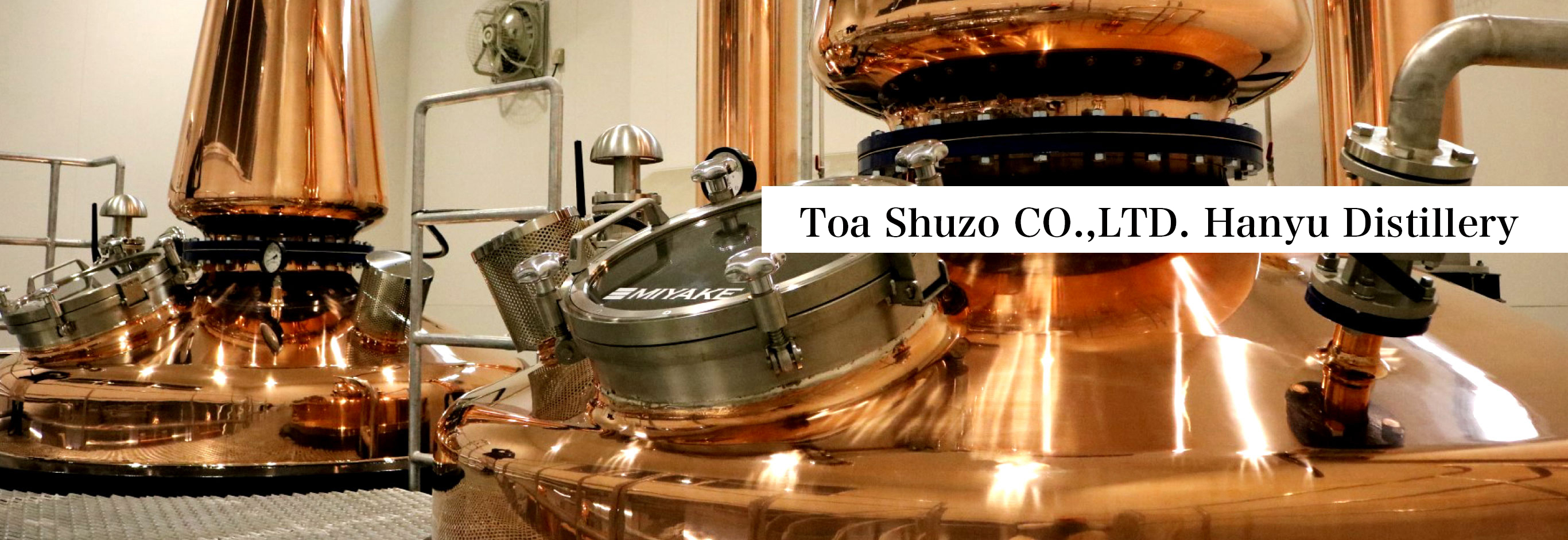
Toa Shuzo resumed its whiskey business for the first time in 20 years at Hanyu Distillery in the city of Hanyu in the Saitama prefecture. MIYAKE, which was contracted to design and manufacture the first pot still of the company, completed the entire process production equipment with the latest specifications while reproducing the original shape.
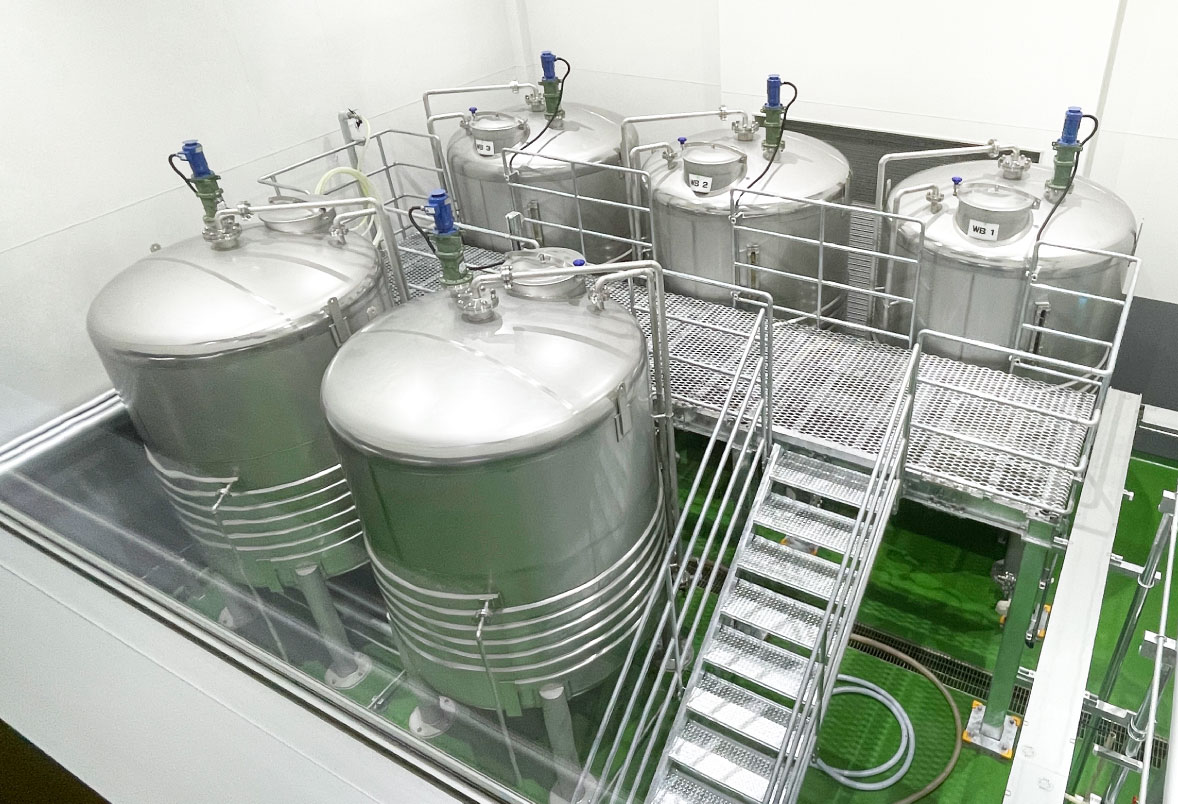
Challenging whiskey production again
after longing to do so for 20 years
Toa Shuzo has a history of nearly 400 years of refined sake production. The company was founded in the city of Chichibu in the Saitama prefecture in 1625 and moved to the current location in the city of Hanyu in 1941. In 1946, the company acquired a license to produce whiskey and launched its whiskey business. It initially sold products that were blended with imported malt whiskey, and, in 1980, opened Hanyu Distillery to work on producing its own malt. However, with the sluggish demand for whiskey, Hanyu Distillery was forced to shut down in 2000 and then was constrained to suspend whiskey production in 2004.
“We want to challenge whiskey production again someday.” This strong desire of theirs was finally realized with the advent of the whiskey boom in recent years. The company contacted MIYAKE, which manufactured its original pot stills, because it still had some of the employees working actively at the distillery before the shutdown and had kept the hand-drawn drawings of the original pot stills. Finally, Hanyu Distillery was restarted, their first step on the road to recovery after 20 years.
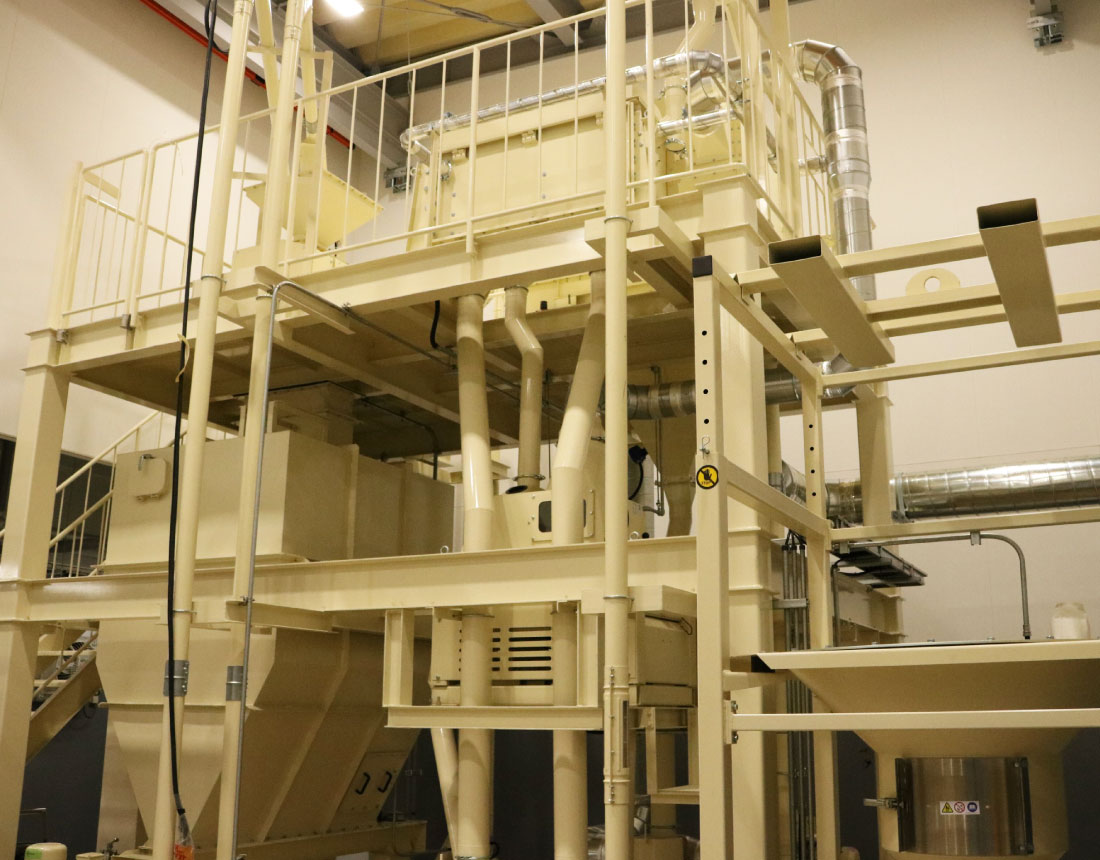
MIYAKE’s sophisticated technology is still alive in the details of its process production equipment
The planning of the reopening of Hanyu Distillery was started in 2017, and, in July 2019, we received the order. It was completed in February 2021. In the planning stage, we made proposals using drawings and other materials and proceeded with the plan while confirming their details. We were contracted for the equipment for process production from malt crushing to mashing, filtration, fermentation, and distillation.
For the malt crusher, we introduced equipment manufactured by Künzel in Germany. Although it is not our product, we are able to undertake the assembly and maintenance of the machine.
The rest of the equipment is our unique custom-made products. For the mashing tank (Lauter tun), we also manufactured the filtering screen, which is an important part. The screen has a special function on the cross-section of its slits, which prevents solids from passing through and allows liquids to pass through. For the fermentation equipment, stainless steel tanks with cooling jackets are available, such as the fermentation tank (wash back) and Yeast tank.
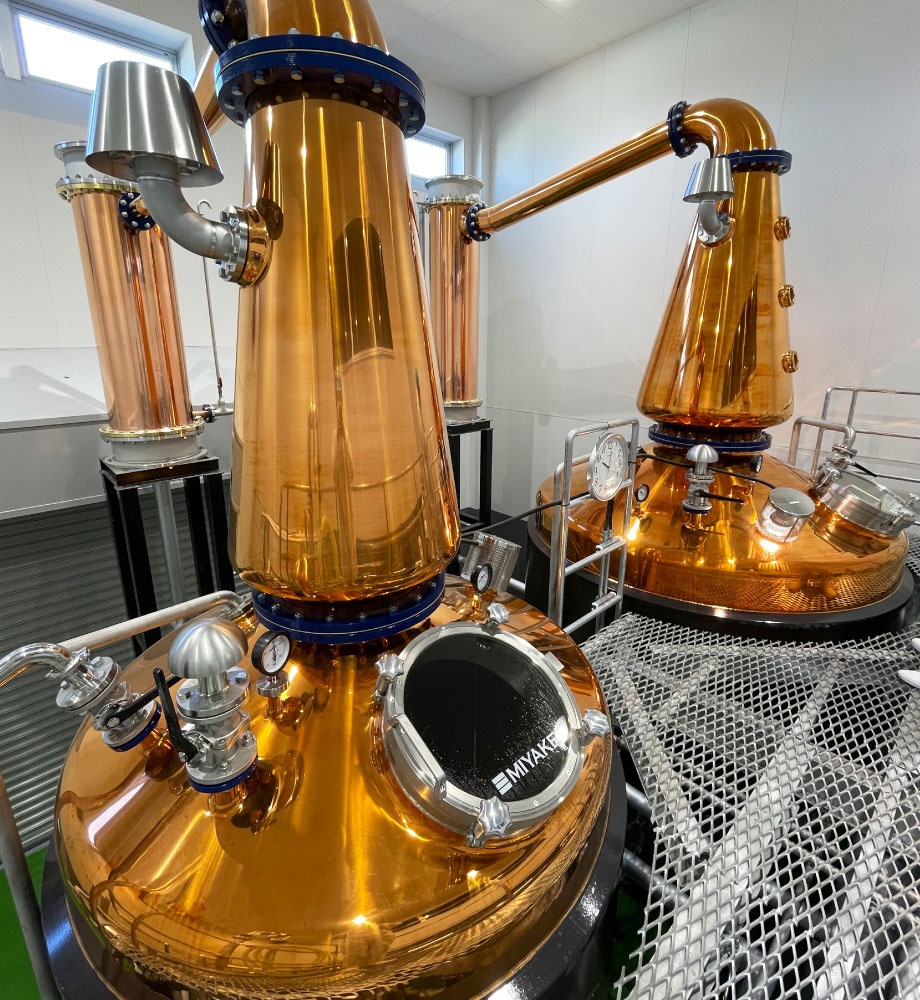
Reproducing the original pot stills with the latest specifications and ease of use
The distilling equipment (pot still) is the key to whiskey production, since the still shape and the pipe angle determine the taste of whiskey. We reproduced two types of pot stills (wash still and spirit still) in their original shapes. They are copper tanks with double-cylinder heaters called percolators that reflect the latest specifications in the layout and arrangement of parts. We are the only company in Japan with the ability to undertake the manufacture of such process production equipment as a whole. It is also our strength to be able to provide post-delivery maintenance and troubleshooting quickly.
In November 2020, we completed the pot stills and started commissioning. Then, after crushing and mashing malt, the distillery started distilling using the wash stills in February 2021. Although the production of whiskey is complete after aging, to begin with, it sold a limited number of new pots just diluted and received purchase orders from many whiskey lovers.
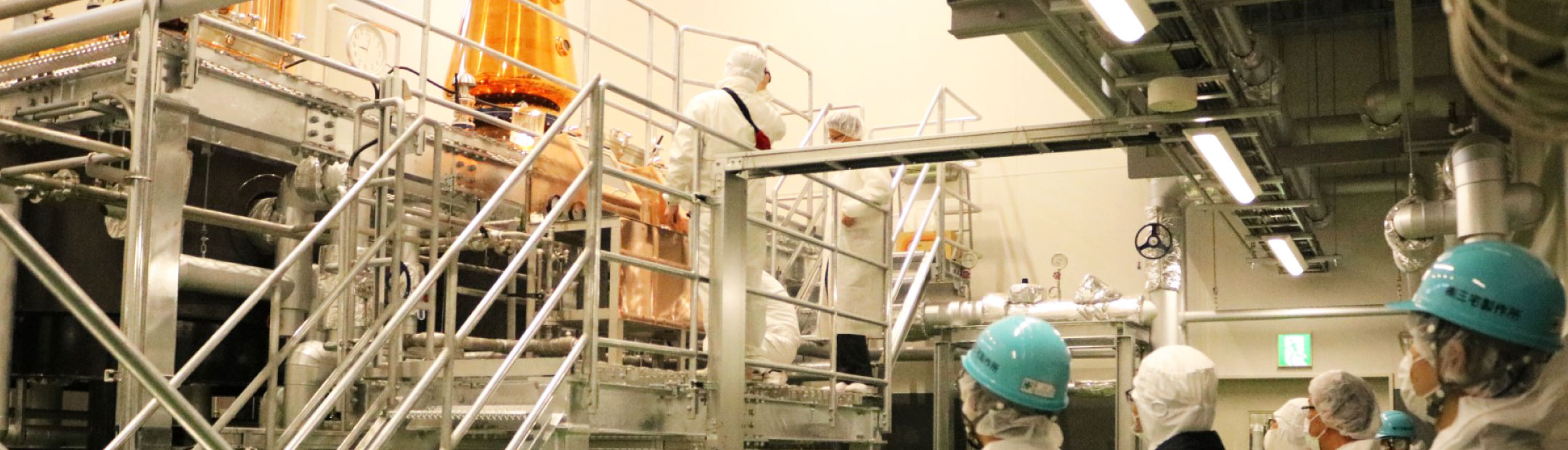
Voices of gratitude from the customer include: “Although the reproduced pot stills have the same shape as that at the time of founding, they are the latest equipment with improvements in layout and arrangement of parts and facilitates our work” and “The partially automated system has made our work easier.”